A Culture of Continuous Improvement with Kaizen
Why your business shouldn't be making change just for change's sake
The Japanese manufacturing industry is renowned for its methods of process improvement. It introduced us to methods such as Kanban and Lean. Another approach that’s proven to be popular amongst businesses that want to improve how they operate is Kaizen.
In this article, we’ll discuss what Kaizen is, and how it can steer your business towards continuous improvement.
What Is Kaizen?
Kaizen is an approach that encourages an entire company to work together to achieve continuous improvement. It believes that change happens iteratively instead of in big, drastic moments.
Contrary to popular belief, the word itself does not mean “continuous improvement”. Continuous improvement is actually a result of Kaizen. A better translation would probably be “change for the better” as it advocates making a change that has an effect instead of change for change’s sake.
The History of Kaizen
The concept of Kaizen was developed in the Japanese manufacturing industry after World War II. Although many companies implemented this approach to their businesses, it was at Toyota that this way of working really stood out.
The Toyota Production System (TPS), the very system that brought us Lean manufacturing, highlights Kaizen as one of its main principles. TPS is a set of management practices and philosophies developed by the car manufacturer that stresses continuous improvement in quality, technology, processes, company culture, productivity, safety, and leadership.
Kaizen’s aim is to improve standardized processes so as to eliminate waste. By eliminating waste, not only can you achieve a more efficient workflow, but also reduce costs and enhance customer value.
In 1986, Masaaki Imai, an organizational theorist and management consultant, introduced and popularized Kaizen to the Western world. Both through his book, “Kaizen: The Key to Japan’s Competitive Success” and the consulting institute he founded called Kaizen Institute Consulting Group (KICG), Imai familiarized companies outside of Japan with the concepts, systems, and tools of Kaizen.
Key Elements of Kaizen
According to the KAIZEN™ Institute, there are five fundamental principles of Kaizen. They are:
- Know your customer: this is about establishing customer value so you can give them an improved experience.
- Let it flow: the primary aim of everyone in your company should be to eliminate waste.
- Go to Gemba: “Gemba” translates to “the actual place” and this principle highlights that value is created only when things actually happen.
- Empower people: this is self-explanatory, you need to provide the right resources to your team so they can succeed.
- Be transparent: you need concrete evidence to demonstrate performance and improvements.
Improve your day-to-day tasks!
As previously mentioned, a result of Kaizen is continuous improvement. By introducing your company to the concept of Kaizen and taking on board its principles and values, it can steer them towards adopting the approach of continuous improvement in their day-to-day operations.
Understanding the Benefits of Continuous Improvement
Developing a culture of continuous improvement can be beneficial. Here are some examples of how it can help your business operate on a higher level:
1. Customer Satisfaction
As one of the key elements of Kaizen, knowing your customer can lead to providing them with a better experience. The nature of continuous improvement challenges workers to always look for ways to enhance their workflows. This can result in better product alignment which helps to better recognize customer values.
2. Better Engagement
Customers aren’t the only ones who benefit from a continuous improvement culture, businesses themselves will find that it can also engage employees better. The basis of continuous improvement encourages all workers to identify flaws in processes and assess how to make it better, and if successful, share and implement it throughout the entire company. This can motivate workers to engage more in what they’re doing and create a culture of proactive learning.
3. Improved Efficiency
It comes as no surprise that incremental improvements can add up to improved efficiency. Not only will processes become more streamlined, but it can enhance the distribution of resources and reduce costs. If one of your primary objectives is to eliminate waste, your production costs can go down as well. Waste in processes is costly, and even the smallest of improvements can influence the overall cost of a business.
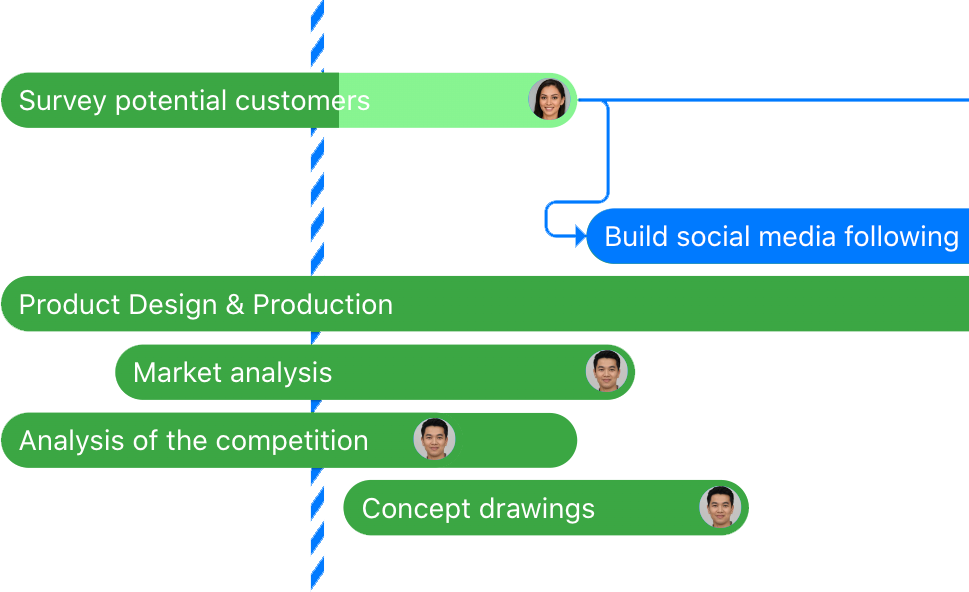
Creating a Culture of Continuous Improvement
There are various ways you can create a culture of continuous improvement. Here are some of the more common ways of implementing it as according to the Kaizen concept:
1. PDCA
PDCA stands for Plan → Do → Check → Act and it is a method used in business to spur continuous improvement of processes and products. Also known as the Deming circle or the Shewhart cycle, it follows a sequential order of stages which are:
- Plan: Set up goals and requirements that can deliver the desired outcome.
- Do: Carry out what was outlined in the planning phase and collate data to see whether the change has made an impact.
- Check: Evaluate the data that was collected from the do phase and make changes or improvements to the process accordingly.
- Act: Take measures to improve the process.
2. 5 Whys
5 Whys is a problem-solving technique that gets to the root cause by asking the question “why?” five times. It proposes that by asking the question five times, you can get to the solution of your problem and it should ideally direct you to a process.
Here’s an example of how it works. The problem: There is no coffee available in the office.
- Why? → Because the coffee machine is not working.
- Why? → Because it hasn’t been properly maintained.
- Why? → Because the person who usually does it is on vacation so no one has been doing it.
- Why? → Because a replacement person was never allocated.
- Why? → Because the person in charge forgot to allocate a replacement.
Here we found out that the root cause was because managers forgot to assign a replacement for a vacationing employee. To avoid future mishaps in this area, we now know to ensure that there should always be someone responsible for the maintenance of the coffee machine.
3. Kaizen Event
A Kaizen event, also known as a Kaizen blitz or Kaizen burst, is a workshop-like event that focuses on process improvement. Often facilitated by someone in the implementation team, it includes training, analysis, and design of an area of business that requires enhancement. An event can take up to 10 days and tools such as process mapping are involved.
While these one-off events can be beneficial, it should be noted that they should only be part of an overall continuous improvement strategy for true effectiveness.
Final Thoughts
Even if your business is doing well, there’s always room for improvement. One of the biggest gains of continuous improvement is that it can achieve a huge change over time. But it doesn’t come easily. Whichever method your business decides to implement, remember that it takes time, practice, and consistency for it to have a true effect.
Does your business practice continuous improvement? If so, let us know which method you use!
Cheers,
Dinnie and the Zenkit Team
FREE 20 MIN. CONSULTATION WITH A PROJECT MANAGEMENT EXPERT
Wanna see how to simplify your workflow with Zenkit in less than a day?
Book a Live Demo